September 5, 2019 | Sandy Giardi
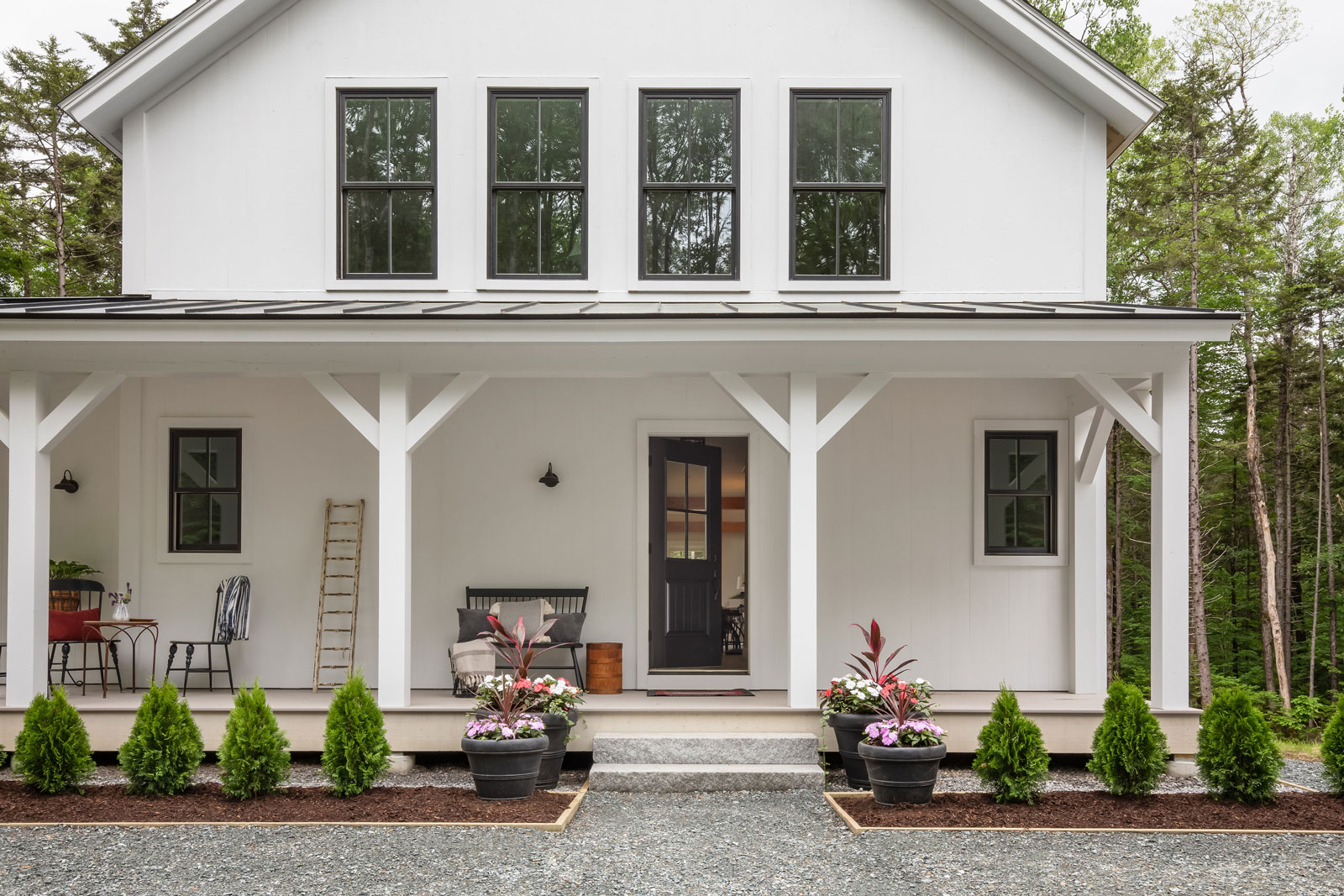
Yankee Barn Homes in Grantham, NH, recently celebrated 50 years in business, and, to celebrate this golden anniversary, they invited Yankee Barn Home owners to the Eastman community for tours of four Yankee Barn Homes and a reception at their newest model home, The Springfield Barn Home. Fittingly, about 50 Yankee Barn Home owners came for the occasion, shares Yankee Barn Homes’ Co-Owner and Creative Director Jeffrey Rosen, armed with scrapbooks, photographs and more than a little admiration for their beloved post and beam homes. To have an entire room full of YBH owners at once was gratifying, says Rosen, and their collective passion for the constructs they call home, inspiring.
Since the company’s inception in New Seabury on Cape Cod (the company relocated to Grantham in the ’70s), Yankee Barn Homes has built 1463 homes, yet today only takes on 16 to 20 projects a year to maintain that “American-made, hand-crafted” approach the company champions. The technology used for the energy-saving components of a Yankee Barn Homes build, however, is cutting-edge.
The Downing Barn Home
Yankee Barn Homes has evolved from a handful of designs to a sky’s-the-limit approach, where clients can use YBH’s post and beam styles—think Carriage Houses, Barn Homes, Mountain Homes and Coastal Homes—as launchpads for their own customized timber frames. “We want people to realize,” says Rosen, "that prefabricated doesn’t mean you’re stuck into one specific style and that a [Yankee Barn Home] is completely custom.”
Laurel Hollow Barn Home
Today, the designers at Yankee Barn Homes can design and manufacture almost any architectural style. In fact, two years ago, the company successfully created a rebuild of a turn-of-the-century Nantucket cottage that had tragically been lost to a fire. Ultimately, the clients received an energy-efficient and green build with all of today’s modern conveniences—though the cottage bears a striking resemblance to the one that came before it.
Clients work with Yankee Barn Homes designers either at their Grantham location or via GoToMeetings, which allow homeowners to see the plan for their dream home materialize and evolve in real time in three dimensions, on their computer screen. If you were to say you’d like to add another window on a given wall, you'd be able to see that change immediately. Once fabricated, a Yankee Barn Homes shell package, consisting of their trademarked wall and roof panels and the post and beam structural frame, is delivered to the property site for assembly, saving both time and job waste. Yankee Barn Homes' shell packages are generally assembled in 10 days or less.
Yankee Barn Homes' Granite Ridge design
Every year, Yankee Barn Homes shows a model house in New Hampshire, explains Rosen, “because once you get somebody into a post and beam structure, the structure speaks for itself.” After all, the merits of a post and beam home—the vaulted ceilings, open floor plan, generous use of glass, inherent green qualities, indoor-outdoor connection—have long held appeal and show no sign of stopping.
Fifty years ago, Yankee Barn Homes debuted The Mark 1, which was fairly contemporary for its time. This year, they’ve unveiled the Springfield Barn Home, what Rosen refers to as “a big little house,” that is sure to resonate with a variety of people.
Springfield Barn Home
The white structure with black windows, board siding, lots of exterior glass and a dual cupola (shown above and top) answers the current movement for farmhouse and barn-style housing with an open-plan design that delivers the best of both worlds. It is as heavy on curb appeal as it is on utility and storage. Says Rosen, “As a designer myself, I’m always trying to push the envelope in terms of what we’re doing. We hang on to everything that people love about us, which is the post and beam and some of the traditional architectural shapes, but we try to push the concepts of how you live in these spaces.”
Main image: Springfield Barn Home
Add new comment